Is anti-‘sweatshop’ activism making Bangladeshis poorer?

One of the worst industrial disasters in the modern era took place in Bangladesh when the Rana Plaza garment factory collapsed on April 24, 2013, killing more than 1,100 people and injuring some 2,500.
Following the disaster, new safety and inspection agreements were put in place. But 10 years later, it seems that these safety standards slowed the growth of the garment industry, which is the primary path out of extreme poverty in Bangladesh.
The media coverage of the disaster spurred worldwide anti-“sweatshop” activism. This led to unprecedented coordination among anti-sweatshop activists, unions and multinational textile buyers to create, monitor and enforce improvements in working conditions in Bangladesh’s garment factories.
The Accord for Fire and Building Safety and the Alliance for Bangladesh Worker Safety are two separate, though similar, agreements under which major international buyers agreed to source garments only from factories that met the safety standards laid out in these agreements. The Accord was associated with international brands from more than 20 countries across four continents, while the Alliance consisted of mostly North American firms such as Gap and Walmart.
The agreements’ safety standards essentially substituted for government regulations. Jointly, the standards covered approximately 40 percent of Bangladesh’s garment factories and 75 percent of its garment workers.
Unlike government regulations, which often go unenforced in poorer countries, these agreements have been enforced. Violations of Accord standards have led to
156 factory closures, while Alliance buyers have terminated purchases from 97 factories.
While a disaster on the scale of Rana Plaza has not occurred since these agreements were put in place, the increased safety isn’t free. Multinational companies have paid for monitoring, and Bangladeshi firms are responsible for financing any safety improvements deemed necessary. Unless these improvements have increased workers’ productivity proportionate to their cost, the increased safety has raised the cost of employing Bangladeshi garment workers.
When the cost of Bangladesh’s labor increases relative to its productivity, standard economic theory predicts that it will shift business away from these workers and towards their substitutes — in this case, labor in other countries that is more productive relative to its cost.
Economists Kevin Grier, Towhid Mahmood, and I recently investigated how the reaction to the Rana Plaza disaster has impacted garment-industry employment and company growth. We
found that employment was 28 percent lower and that there were one-third fewer garment factories than there should have been compared to the relevant counterfactual expected growth.
This is important because the garment industry has been a major pathway out of poverty in Bangladesh. At the time of the disaster, Bangladesh was the world’s second-largest textile producer (after China), employing roughly 4 million, mostly female, workers. The wages they earn, while low by U.S. standards, are relatively high in Bangladesh.
In other recent research, which I will present at a conference on Monday, my co-authors and I found that wages in firms singled out in the press as harmful sweatshops averaged $6 per day in Bangladesh during the 2010s. That may not sound like much to U.S. readers. But during that same period, nearly 87 percent of Bangladesh’s population lived under the World Bank’s $6.85-per-day extreme-poverty standard, and 52 percent lived under $3.65.
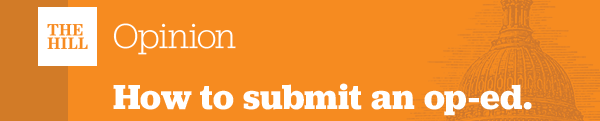
Economic development ultimately raises both worker pay and factory safety standards. There is some evidence that this process has been improving pay in Bangladesh, even among so-called sweatshops. Our research notes that reported sweatshop pay doubled in the most recent decade over the sweatshop wages reported from 1995 through 2010.
Development in the United States, which raised wages and improved working conditions, played out during the Industrial Revolution, and it is proceeding today in Bangladesh. Unfortunately, while the reaction to the Rana Plaza disaster may have spurred the adoption of greater safety standards, it may have also slowed the country’s economic progress.
Benjamin Powell, a senior fellow at the Independent Institute in Oakland, Calif., is director of the Free Market Institute and a professor of economics in the Rawls College of Business at Texas Tech University. He is author of “Out of Poverty: Sweatshops in the Global Economy.”
Copyright 2023 Nexstar Media Inc. All rights reserved. This material may not be published, broadcast, rewritten, or redistributed. Regular the hill posts