How to narrow construction’s big, and growing, labor gaps

The U.S. construction labor shortage is bad, and getting worse, with a record 440,000 job openings, plus another million in manufacturing.
Who will do the work envisioned in the $1.2 trillion 2021 Bipartisan Infrastructure Law? This isn’t just about construction sites; about half the labor shortage will affect engineering and materials before work can even begin.
Any shortage can cause delays, drive up costs and even mean cancellations. In addition, because of inflation, the longer the United States takes to solve the problem, the less building it will get for the buck because the money shrinks in real terms.
Today’s mismatches stem from structural shifts in the U.S. labor market. Though the economy has shrunk for two straight quarters, unemployment is low, at 3.5 percent, and there are 10.7 million unfilled positions. Moreover, even if the United States officially enters a recession, construction-related demand for labor is not likely to shrink, because much of the spending in the infrastructure law, as well as that of the private sector, is locked in.
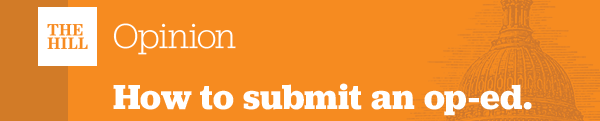
Four broad actions could help close the widening gap between labor demand and supply.
- Increase the supply of labor. Reskilling and upskilling is a no-regrets move all around, and there is demand for it: 58 percent of workers in construction say they plan to pursue future training, education or credentialing. There are many examples, such as state requirements to offer on-the-job training and online platforms that link employers, educators and applicants. There could be more. The bigger opportunity is to bring more people into the industry. There are almost 4 million Americans who say they want to work but have not sought a job in the last year. Luring them in means offering a solid employee value proposition. That may require thinking more imaginatively than has been typical, such as developing and offering affordable housing and day care. The latter could be particularly attractive to the 2.1 million women who want to work but are out of the labor force, and who are seriously underrepresented in the sector, as are African Americans. This is not cheap, but the cost of not having enough labor could well be higher. The formerly incarcerated are another potential — and largely untapped — source. They are much more likely to be unemployed or to have a series of low-paid, insecure jobs and would certainly benefit from access to long-term opportunities. It would also be helpful to present the industry as what it is — not just guys in hard hats wielding big tools, but a sector of many differently skilled, well-paid jobs that offers satisfying careers. Work with high schools to get students thinking about a career in the industry — whether that is in an office, in the trades or in management — when they are young. Ohio’s High School Tech Internship Pilot program, for example, brings awareness by allowing employers to hire high school interns. Helmets to Hardhats seeks to bring military veterans into the industry.
- Improve productivity. This is also easier said than done. Indeed, labor-productivity growth in construction has been glacial for decades. In particular, the sector has been a slow tech adopter, even though technologies like digital design and the automation of material-production processes could help offset the workforce challenge. Modernizing the tech stack would have the added benefit of attracting a new demographic of skilled talent. Offsite manufacturing is also associated with improved productivity, but uptake in U.S. markets has been limited. In addition, there is often room to improve job site management. Working with agencies to “dig once,” rather than incur multiple excavations, uses both labor and supplies more efficiently.
- Rethink how to work with contractors and suppliers. In a world of rising inflation and uncertainty, the practice of lump-sum, fixed-price contracting with the lowest price winning can lead to inflated bids, with contractors pricing for worst-case scenarios. This can lead to less and/or lower-quality infrastructure. It is, therefore, worth exploring other kinds of contracting protocols, such as reimbursing contractors for labor and material spending as the project progresses, or “collaborative contracting,” in which both parties waive their rights to sue. There may also be ways to improve specific terms and conditions. For example, some states award a bundle of small construction projects and allow the contractor to execute over a flexible time horizon and sequence. And it bears looking into how to make it possible for owners to solicit feedback to determine ways to make a project better — something that cannot typically be done under hard-bid procurement.
- Be specific and act fast to get ahead of projected labor shortages. The dynamics of labor shortages are poised to play out unevenly. For example, when it comes to materials, the strain is projected to be greater in places, such as Ohio and Texas, that manufacture and export materials to other states with limited manufacturing capacity. Occupationally, within each part of the value chain, a few jobs are critical and, if left unfilled, can cause serious bottlenecks. In the engineering and technical services subsector, civil engineering is one such “crucible occupation” — and because engineers take so long to educate, a gap not only takes considerable time to fill but can produce outsized downstream consequences. Welding professionals are set to be in demand both in material production facilities and on the job site. And among contractors, operating engineers and line installers are expected to be in particular demand. The recent Inflation Reduction Act, which allocates $369 billion to energy and climate change initiatives, and the CHIPS Act, which supports semiconductor and advanced manufacturing, will likely increase the demand for skilled labor. So there should be a sense of urgency.
Failing to act has consequences. Construction can help to foster the sustainable and inclusive growth that the United States needs; that is unlikely to happen if the labor gaps go unfilled. Moreover, the country will not get the infrastructure the bipartisan infrastructure law is intended to pay for — with consequences both for the economy and for the quality of our lives.
Garo Hovnanian is a partner in McKinsey & Company’s Philadelphia office. Adi Kumar is a senior partner in Washington, D.C.
Copyright 2023 Nexstar Media Inc. All rights reserved. This material may not be published, broadcast, rewritten, or redistributed. Regular the hill posts