‘Internet of things’ can boost US manufacturing might

The “internet of things” offers the potential to connect trading partners, production facilities, products and consumers in ways that can provide visibility and value up and down the supply chain.
Within the manufacturing enterprise, the “industrial internet of things” and related technologies represent a disruptive change to long-established practices, required skill sets and technologies in manufacturing.
The industrial internet of things is poised to change the way many products are distributed and produced. For some, it will offer the opportunity for true mass-customization and the ability to more efficiently produce customized products.
{mosads}For most, the industrial internet of things will result in a factory that is incrementally more adaptable to market changes, more visible to the entire enterprise and more efficient overall. In both cases, however, jobs and economic growth will hinge on successfully adopting these new technologies and the new business practices that will result from them.
Recognizing how impactful these changes are likely to be, governments, academia and industry groups around the world are rushing to develop policies, standards and explore best practices for industrial internet of things implementation — and the U.S. is no exception. To be successful, it’s critical that the U.S. emerges as a leader in this transition to new technologies.
Zebra Technologies, the market leader in mobile computers, scanners and barcode printers enhanced with software and services to enable real-time enterprise visibility solutions, recently conducted a survey of 1,100 manufacturing executives around the globe.
The study analyzed the emerging trends shaping the future of industrial manufacturing. Not surprisingly, the findings indicate that the industrial internet of things is one of the key technologies manufacturers are looking to for success.
Respondents cited their priorities as increasing production while adapting to a changing market that is expecting customized products and short delivery times.
What’s driving their technology investment plans?
- Meeting growing demand
- Increasing needs for customization
- Faster time-to-market
- Increasing supply chain complexity
These customer-driven requirements are non-negotiable for manufacturers today. But how can manufacturers leverage new technology to achieve these goals? Along with the industrial internet of things, enabling technologies like voice-recognition, radio-frequency identification (RFID), wearable technology and location-tracking solutions are top priorities for investment.
Accordingly, the adoption of these technologies is shifting the nature of jobs and required skillsets, but not slowing job creation.
The top industrial internet of things benefits expected include:
- Optimizing production
- Improving quality
- Greater visibility to operations
- Better operational flexibility
These changes will, of course, impact employment and the mix of jobs in the economy. According to a recent report from the United States Department of Commerce, U.S. manufacturers have added nearly 950,000 jobs since 2010.
By leveraging proximity to market and customer-specific products, the industrial internet of things will lessen the advantage that comes from low labor costs. From a global perspective, this change will continue to attract manufacturing closer to the U.S.
Within the manufacturing enterprise, some legacy jobs will be impacted as information gathering, aggregating and analysis tasks become automated. Other jobs, generally higher in skill, will be created in software, engineering and analytics.
Integrating these new sensor- and analytics-based solutions will require deep domain knowledge and skills. It is critical the U.S. lead in the adoption of these new practices and technologies to remain competitive on the global stage.
Finally, the trends, plans and opinions would not be as positive were it not for the positive growth climate. The macro expectation for growth and new manufacturing sets a very positive stage. As recently as 2008, the trend to accomplish “more with less” was restrictive.
With the current pro-growth climate surrounding this 2017 study, utilizing IIoT to accomplish “more with less”, adopting the principles of Industry 4.0 to achieve expanded actionable visibility and other stated trends all point to progressive investment.
Smart decisions can be made by smart factories adopting new technologies with real-time location systems (RTLS) and expanding traditional RFID, wearables and Software as a Service (SaaS) platforms.
As savvy manufacturers invest in technologies that will create a smarter, more connected plant floor to achieve greater operational visibility and enhance quality, the future of the manufacturing industry — and the jobs that will be created — looks bright.
Mark Wheeler is the director of supply chain solutions for Zebra Technologies, which manufactures and sells marking, tracking and computer printing technologies. Its products include thermal barcode label and receipt printers, RFID smart label printers/encoders/fixed & handheld readers/antennas and card and kiosk printers that are used for barcode labeling, personal identification and specialty printing, principally in the manufacturing supply chain, retail, healthcare and government sectors.
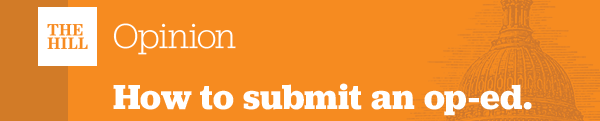
The views expressed by contributors are their own and not the views of The Hill.
Copyright 2023 Nexstar Media Inc. All rights reserved. This material may not be published, broadcast, rewritten, or redistributed. Regular the hill posts